1. Introduction
In today’s fast-changing world of making things, ‘going digital’ is an important consideration for companies. This transformation is not just a trendy term; for many it’s a ‘must-do’ to keep up and do well in the modern market using technologies to improve productivity. Digital transformation means changing how we do traditional manufacturing by using digital technologies with security at its heart. It’s all about making operations more efficient and effective in our connected world.
Digital transformation is like a stepped change that companies can’t ignore if they want to do more than just survive. It’s a key move to thrive and succeed in a world that’s always changing with new technologies. As we talk about this topic, it’s crucial to understand why digital transformation is ‘game-changing’ for manufacturers trying to remain competitive in the industry.
Going digital brings lots of benefits. It can make things run smoother, improve the quality of products, make customers happier, keep employees satisfied, keeps you informed and in control of your processes and even helps the environment. These advantages come from using smart technologies in a thoughtful way.
Be aware there is no golden bullet despite what many of the software vendors would have you believe, you must start from good foundations and this article will discuss this in more detail later. Things like figuring out how to use new technologies, dealing with costs, finding the right people with the right skills, making changes in company culture, worrying about security, optimising processes to reduce waste and collecting & managing data effectively are some of the hurdles to overcome.
So, why are we here? This article is here to help leaders in manufacturing, just like you, navigate this digital transformation journey. We want to shed light on the complexities, opportunities, and challenges that come with this shift. Our goal is to give you the insights you need to make smart choices and lead a successful journey into the digital age.
In the next parts, we’ll break down what digital transformation in manufacturing really means, look at its different parts and provide practical tips to help leaders like you reach excellence in the digital world.
2. What are the potential outcomes of industrial digital transformation?
There are many different outcomes of applying digital solutions in the manufacturing environment, which we shall list later, but a better question could be “what are our biggest business challenges and can industrial digitalisation help improve them?” The answer to this question is most likely ‘yes’.
Whilst every business is different, and yours will have unique challenges, the most common business improvement areas include:
- High energy costs, with little analysis and no insight into how to reduce costs,
- Low productivity or production efficiency,
- Unacceptable scrap and waste levels,
- Unexpected or unplanned machine or line down-time,
- Manufactured quality tolerance creepage,
- Inadequate traceability of product to process measurement and
- Manual systems, such as: production planning and inventory tracking.
All of the above points can be monitored and improved in real-time with the application of digitalisation methods. The resultant outcomes from addressing some of the items above will be clear to the reader, but beyond the obvious profit impact of lower costs, there are additional benefits such as:
- Reduced negative environmental impact from waste energy and process emissions.
- Improved flexibility brings a stronger competitive edge.
- Higher quality and more reliable production lead-times to improve customer satisfaction.
- Accurate traceability and validation can help develop new markets and reduce risk.
- Reduced capital expenditure costs due to improved utilisation and maintenance of machines.
- Improved production efficiency due to effective production planning.
- Real-time manufacturing shopfloor visibility for greater team engagement.
Expert advice:
Whatever your reason for embarking on a digital transformation project, bear in mind the other challenges you may want to extend it to. Ensure that you develop a single holistic solution for all future improvement areas, that shares common network architectures and data storage solutions.
3. How do you begin the journey?
This journey can be a long, and to some, a daunting journey when you first look at the challenge, however, it’s like any other project undertaking and should come as no surprise to you, as you’ve probably tackled a few in the past.
The beginning:
Start by knowing your destination, ensuring that your company has a well-defined and agreed set of objectives in support of your vision. Then identify your ‘need’ and your ‘reason(s)’ for doing this project. Always link your actions back to the problems you are addressing by embarking on this digital journey.
A digital transformation project needs to be driven by its leaders. We can’t stress this enough, projects fail when active leadership and sponsorship is absent.
In any digital transformation journey, there are three key areas of focus:
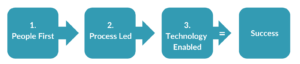
People are key and are the primary focus on the digital journey, from organisational structure, organisation culture, skills, tacit knowledge to buy-in at all-levels. This means that Change Management is an important component in the transformation journey.
Your manufacturing is driven through your processes and it’s these processes that need to be efficient and streamlined, before implementing technology. Discuss and capture all manufacturing processes to be streamlined and optimised to minimise waste.
Lastly, technology, this is merely an enabler, not the golden bullet as some would have you believe, it is a tool that helps bring about visibility, transforms data into information, connects your manufacturing world to bring about control and insights you may not have previously known about. It’s important to note that technology alone is not the solution to achieving a successful digital journey.
However, it’s also important to recognise that success lies in balancing all three aspects—People, Processes and Technology. Neglecting one can result in suboptimal outcomes, resulting in wasted resources and missed opportunities for growth.
The organisation’s digital transformation must align with the company’s mission and vision.
Craft a detailed plan outlining each step of your digital transformation. Assess the financial aspect; understanding the costs involved and securing sufficient support for project completion. Consider seeking guidance from experts experienced in digital transformations to ensure proper implementation. Remember, a successful transformation requires a thorough understanding of the current state, defining the target state and identifying gaps in People, Processes and Technology.
4. Steps to Calculate ROI for Digitising Manufacturing Operations?
Calculating the Return on Investment (ROI) is so important and so many organisations fail to revisit this along with Payback Period where the amount of investment, can be recovered within months or years by cost reductions or other savings (e.g. energy or scrap) in production.
If we assume that the investment costs, are the total costs of a digitalisation project in your factory, then the total costs are made up of your direct and indirect costs. Direct costs associated with digitisation, include, software, hardware, consulting fees, training expenses and any initial setup costs. Whereas indirect costs may involve potential downtime during transition, temporary decreases in productivity during the learning curve and any unforeseen expenses.
Benefits and savings:
The estimated net benefit is calculated by identifying increased efficiencies, quality improvements, cost savings and new revenue growth. Such improved efficiencies and savings may include:
- Faster production cycles,
- Reduced lead times,
- Enhanced resource utilisation,
- Quality improvements leading to fewer defects,
- Reduced waste & scrap and
- Reduced energy consumption
Try to assign monetary values to each benefit where possible, example: calculate the cost savings per unit produced, estimate the potential revenue increase or assign a value to time saved through increased efficiency.
The uncertainty of ROI from an industrial digitalisation pilot:
In any industrial digitalisation pilot project, calculating the Return on Investment (ROI) or Payback Period can be a challenging task. The primary motivation behind such projects is to leverage previously inaccessible data combining data to provide users multi-dimensional insight to enhance business efficiencies and overall performance.
What we find is that for many manufacturers the exact savings and the exact costs, cannot be understood until after a project has been completed. Try to ask yourself how much productivity improvement (or energy saving) could we realise, if only we knew where our productivity losses (or energy wastage) were in our business or plant? Not easy, I am sure you will agree.
If this is the case, you might need to make some assumptions and or set some targets for what a reasonable saving (as a percentage) could be, if only you knew where your inefficiencies were.
For example, if you have a perceived OEE of 65% and a belief that by improving this to 75% you might realise an annual benefit (released capacity opportunity or cost saving) of £100,000 then it may be worthwhile in embarking on a digitalisation project costing you £50,000. This is against a backdrop of most companies incorrectly calculating their OEE and often overstating it by significant values due to lack of reliable data.
Trust your people, trust your judgement, select the right partner and see those savings drop through to the bottom line.
5. Who to involve (internal and external)
Let’s dive into the nitty-gritty of building your dream team for this digital revolution, including both internal champions and external allies. We’re not just talking about your average team here; we’re talking about assembling a crew that’s ready to tackle this digital transformation head-on and come out on top.
First things first, inside your organisation, it’s time to shake things up. Round up the IT team, the Control Systems Engineers, the Continuous Improvement Engineers and anyone else who’s got the ability to make things happen. It’s like putting together a winning sports team – each player brings their own strengths to the table, and together, you’ve got a powerhouse lineup. Don’t forget about those unsung heroes from the shopfloor who always step up when the going gets tough.
But let’s not stop there; we need to cast our net wider. Externally, you’ll want to enlist the help of competent system integrators and suppliers who are willing to ride the digital wave with you. Bring them into the fold early on, get them on board with your vision and watch as they become key players in your digital journey. Of course, you can’t forget about the tech gurus, the consultants with battle scars and the industry insiders who know the game inside out. They’re like your digital Avengers, armed to the teeth with the tools and knowledge to help you navigate this brave new world. Don’t sleep on the innovators and academics; they’re the ones pushing the boundaries and coming up with the next big thing.
But it’s not just about filling seats; it’s about creating a culture where everyone feels like they’re part of something special. Keep those lines of communication wide open, be upfront with your team and make sure everyone’s got skin in the game. Don’t be afraid to mix things up – a little brainstorming here, some trial and error there, it’s all part of the process.
So, gather your troops and let’s get this digital party started. With the right team by your side, including internal champions and external allies, there’s no limit to what you can achieve.
6. Managing the change as it affects people
Let’s talk about managing change and how it’s going to shake things up for the team. We’re not just talking about moving a few desks around here; we’re talking about flipping the script and ushering in a whole new way of doing things.
First off, for many, change can be scary – no two ways about it. But it’s also a chance to step up our game and show what we’re made of. So, first things first, we have to get everyone on board. That means being straight up about what’s coming down the pipeline, laying out the game plan and making sure everyone knows their role in the new order of things. Communication is key here – we have to keep those lines wide open and make sure everyone’s got a chance to air their concerns and ask questions.
But it’s not just about talking the talk; we have to walk the walk too. That means leading by example and showing that we’re all in this together. It’s about fostering a culture of collaboration and support, where everyone feels like they’re part of something bigger than themselves. A little positive reinforcement never hurt anybody – let’s celebrate those small victories and keep the morale high as we navigate these choppy waters.
Of course, change isn’t always going to be smooth sailing. There’s going to be headwinds and high seas and that’s where we have to be flexible and accept a few setbacks. It’s about adapting on the fly, learning from our mistakes and never losing sight of the end goal.
So, buckle up team – change is coming, and it’s going to be one hell of a ride. But with the right attitude and a whole lot of teamwork, we can weather any storm and come out stronger on the other side.
7. Handling the IT & OT clash (people & processes)
This is an area that all businesses who are planning to embark on an industrial digitalisation project, should plan for in advance, so what is it first:
We all know what an IT department does, they keep our networks, PCs, email traffic and business systems running securely and reliably. Many people are often unaware or neglect the other technologies in factories and rarely have defined teams, yet this technology is at the heart of our equipment and machines. These are known as Operational Technologies (OT).
In simple terms operational technologies are all the control systems, automation systems and industrial computers systems, their software and networks that keep the industrial machines and processes running. In some businesses these departments are a small number of experienced, often quite mature controls or automation engineers whose job it is to make sure that production doesn’t stop and if it does, to get machines and control systems up and running before production generates too much waste or scrap.
So why the clash?
Both teams of people work with computer-based technology, where process failure can be costly to the business. However, traditionally, these two roles have not needed to come together and as such they didn’t need to understand each other’s priorities or work. They have been left alone and trusted in their expertise.
But digital transformation is creating a necessary convergence between the IT and OT functions of a business, or what some call the ‘bridging the IT & OT divide’.
As your teams will inevitably now need to collaborate, expect some members to become defensive or protective of their own activities, but with the right intentions, for example “to make sure that this machine doesn’t stop working” or “to make sure that a virus cannot get onto the control system computer”.
And how to manage the clash?
Building early cross functional teams and employing staff or contractors who understand both sides of the OT/IT divide, will help get everyone involved to understand the wider business challenges and to understand the nuances of each other’s roles and equipment.
Businesses like gunnercooke and InControl Systems can work with your teams to develop the network architectures that satisfy the IT teams, whilst interfacing with process control systems without compromising the machine’s performance.
8. Cyber security is not optional, it’s a given
Let’s dive deeper into cybersecurity because, let’s face it, in today’s digital age, it’s not just an option anymore; it’s a must-have, especially when we’re talking about our factory shopfloors. Think of it like installing security cameras in every nook and cranny – you need to keep an eye on things to prevent any funny business.
Now, cybersecurity might not be the most captivating topic out there, but trust us, it’s a whole lot more captivating than dealing with a data breach or a ransomware attack. So, first things first, we need to take it seriously. That means investing in top-notch security measures, both in our digital systems and on our physical shopfloors. We’re talking firewalls, encryption, regular security audits, and yes, even locking down access to sensitive areas.
But it’s not just about throwing money at the problem; it’s about creating a culture of cybersecurity. That means making sure everyone on the team knows their role in keeping our digital fortress secure, whether they’re on the shopfloor or in the corner office. Let’s not forget about the human element – technology is only as good as the people using it. That means staying on top of the latest threats, practicing good password hygiene and knowing when something just doesn’t look right.
Now, when it comes to our digital networks, we should treat them like Fort Knox. That means segmenting our networks and protecting them like our lives depend on it – because, let’s face it, they kind of do. We’re talking firewalls, intrusion detection systems and regular security audits to make sure everything’s locked down tight.
So, let’s do ourselves a favour and make cybersecurity a top priority, both on the factory floor and in our digital networks. You and your stakeholders will be grateful later when you’re not dealing with a cyber catastrophe.
9. How to drink [& not drown in] the data
Digital transformation in industry is all about getting the data that you need to be able to analyse or respond to, in real-time, in order to be able to improve your business.
To list but a few examples:
- To understand why one machine uses 50% more energy than a similar machine.
- To react [in real-time] to changes in critical machine condition, before it costs you in terms of quality or unexpected downtime.
- To identify root causes for lower than ideal machine productivity (OEE).
Most businesses begin by asking for “all of the data”, so that they can analyse [in their own time] the data using off-line Business Intelligence platforms or MS Excel, but this can quickly lose sight of the benefits of getting the right data, in the right format, to the right places and processes, so that you can begin seeing business improvement opportunities straight away.
Getting the data is often the largest challenge
But getting the data in the first place is often a large challenge*, especially in businesses with legacy or old and unsupported machines & processes. So, the luxury of getting “all the data”, is unrealistic, and ideally you should start by specifying what data you need, so that you can get answers that will help you make adjustments to machines and processes as soon as possible.
(*We suggest you take a look at section 10, to get an appreciation for this issue in more detail.)
Rather than charging head-first at the most obvious business challenge and looking for the data from that process or production line, we would recommend having a long-term plan. This would detail such topics as; how you will create a standard naming convention of data points (e.g. sensor types, location etc.), how and where you will store that data (accessible to multiple business needs) and how you will create a secure process information network.
Getting support for building this plan and architecture for your industrial digitalisation journey, will ensure you meet both IT & OT needs and future proof your systems for the long term. Consultants and contractors such as gunnercooke and InControl Systems Ltd, can support you with this.
10. Machine connectivity, the biggest overlooked barrier to Industrial Digitalisation
Machine Connectivity, what does this mean? In simple terms, most of the data that any business would be expecting to collect, analyse and act upon, resides inside the computerised control systems in your machines, equipment, instruments and process controllers. Yet, gathering that data is a challenge that few recognise, until it becomes a barrier to progress.
Whilst it’s simple to say “network your machines together” the reality is far from simple and needs specialist experience and technologies.
Here are some of the reasons why you are highly likely to meet that barrier:
- Your machines are old, with unknown protocols (if any) and no support from the OEM*
- Your machines are new, yet the OEM wants to pull you into their ‘cloud’ monitoring platform
- Your OEM machine supplier has restricted the access to the network, to only themselves
- Your equipment is controlled by a bespoke embedded controller, with no standard or method of communication.
- Your machine is purely electro-mechanical control, with no internal control system.
(*OEM – Original Equipment Manufacturer)
Firstly, all of these challenges are solvable, but the cost to solve them will vary. From experience we have seen both ends of the spectrum, from a UK OEM who is happy to collaborate with the systems integrator, and the cost is just a few days of work, to the uncooperative major OEM, who wants to charge tens of thousands to facilitate a single machine connection.
Most advanced systems integrators in this sector will have the ability to navigate you through these challenges, but to ensure you make the right decisions that will keep time and costs to a minimum, we make the following recommendations:
Recommendations:
- Create a set of company specifications and standards for control systems and communications (you may need help with this).
- Before procuring new machines or process lines, get a list of requests from your digital transformation systems integrator to write into your procurement contract.
- Ensure that you have the source code and passwords for the control system software on all the machines and processes you own.
- Work with your systems integrator to have a standard ‘machine gateway’ to use with the oldest or most difficult machines and processes. This may involve ‘sensoring-up’ those machines in retrospect.
- Avoid using college and hobbyist technologies to solve these topics, they may be preferred by some as cheap and exciting to use, but they are not widely supported in critical industrial applications.
- Ensure that any equipment used as part of the digital connectivity, uses industry standards, are interchangeable and interoperable, ensuring that you don’t get locked into a single supplier of hardware or software.
Finally, whilst it might seem that this topic is research and innovation led, the above solutions have been deployed in one form or other for many decades from well-established industrial hardware and software providers.
11. Scaling and reaping the rewards
Industrial digitalisation is a transformational journey which some may argue is a process of continual improvement. If you have created a plan at the start of this journey you may have a number of options for scaling and continuing to reap the benefits of the new digital processes that you have already implemented. These options may be:
- To change, adjust and optimise the initial phases of your digitalisation. Applying a PDCA cycle (plan, do, check, adjust) to the first deployments, will be required, especially if you were chasing unknown improvement areas, which often come to light when you begin to see quantified data for the first time.
- Scale the initial project to other machines or process/production lines. For example, if you were using digitalisation to deliver an OEE project, you may want to replicate that success and learning across other production machines, cells or lines.
- Scale your digitalisation project to bring other business benefits. For example, once you have created the network connections to your machines for OEE purposes, you might want to use those same connections for other purposes such as energy monitoring or quality controls.
Be flexible and open-minded
With any digitalisation project in a manufacturing or process environment, you should be prepared to uncover data that may change your perceptions which up until now, may have been based on anecdotal evidence. Alternatively, you should prepare to celebrate those occasions which confirm the ‘gut feeling’ of operators or other staff.
Being flexible with your plans for scaling your digitalisation journey is essential if you are to reap the best financial returns. Indeed, as your business operating climate changes with local and global challenges, you might find new priorities over time. For certain, having designed your network architecture, your data standards and systems correctly in the first place, will allow you to be agile and ensure you gain optimum return on investment for your business.
12. Conclusion
Let’s put a bow on this conversation. Venturing into the world of digital transformation in manufacturing isn’t for the faint of heart, but be prepared, the journey is as exhilarating as it is challenging. By immersing themselves in the intricacies of these critical aspects and embracing the winds of change, CEO’s can navigate the tumultuous seas of digital evolution with aplomb, ensuring that their organisations not only weather the storm but emerge stronger on the other side.
It’s about more than just surviving; it’s about thriving amidst the chaos of technological disruption. The landscape may be complex, but with the right mindset and strategy, CEO’s can unlock a world of opportunities and drive their organisations to new heights of success. So, let’s embrace the digital revolution with open arms and a fearless spirit, knowing that the future belongs to those bold enough to seize the transformative power of today.
About gunnercookeOP
gunnercookeOP are continuously monitoring developments and reporting on many of the identified topics with new articles regularly posted here.
Our mission is simple: to help Investors, Owners, and Leaders grow and improve their businesses. We offer pragmatic solutions that fit your specific requirements, building a toolkit of practices that support performance improvement and the adoption of change.
About InControl Systems
InControl Systems are an advanced process automation systems integrator, who have been deploying OT (operational technology) systems, merged with IT business systems since 1999.
Being able to work at the machine and sensor level of any manufacturing or process site, is an essential enabler for any industrial digital transformation project. Knowledge of current and legacy control systems, networks and protocols is something we excel in.
Many of the topics discussed in this guide are covered in more details on InControl’s website as downloads here.
Should you require further assistance and wish to have a conversation to explore more, contact the authors:
Erol Cacouratos – gunnercookeOP
Ian Clarke – InControl Systems
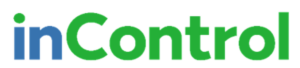